B2 Overview
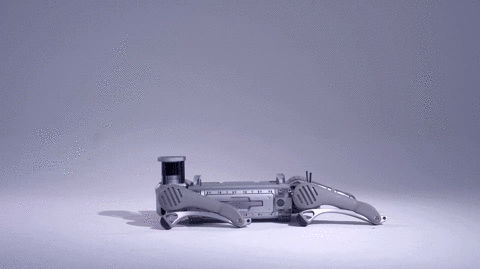
The Unitree B2 is a next-generation quadruped robot designed for advanced industrial, research, and commercial applications. As one of the most powerful quadruped robots developed by Unitree, the B2 combines high mobility, intelligent perception, and exceptional load-bearing capabilities, making it an ideal solution for a wide range of use cases, including industrial inspection, autonomous exploration, logistics support, and security surveillance. Equipped with high-torque joint actuators and precision control algorithms, the B2 is capable of navigating complex terrains with agility and stability. Its robust legged design allows it to traverse uneven surfaces, climb stairs, and adapt to dynamic environments with ease. The robot is powered by an advanced AI-driven control system, enabling autonomous decision-making and real-time obstacle avoidance. The Unitree B2 features a modular and expandable architecture, allowing users to integrate additional hardware such as robotic arms, LiDAR sensors, cameras, and custom payloads to tailor the robot to specific tasks. With a significant payload capacity, it can carry and manipulate objects efficiently, making it suitable for heavy-duty operations. Built with industrial-grade durability, the B2 can operate in harsh conditions while maintaining high performance and reliability. Its long battery life ensures extended operation times, and its wireless connectivity options allow seamless integration with remote control systems and cloud-based data processing. With its blend of power, adaptability, and intelligence, the Unitree B2 sets a new benchmark in quadruped robotics, providing industries, research institutions, and businesses with a highly capable robotic platform to enhance automation, efficiency, and innovation.
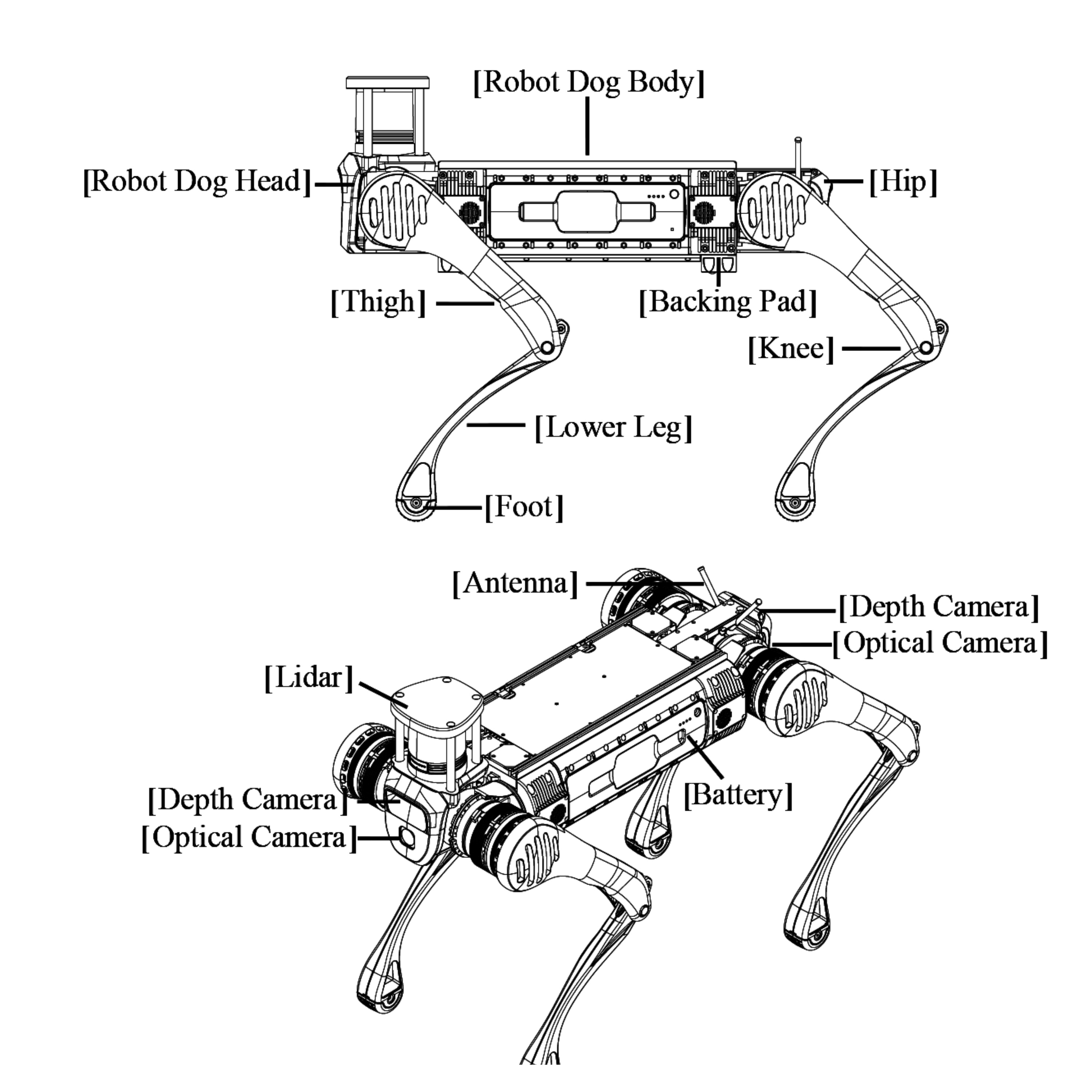
B2-W Overview
As a wheeled variant of the Unitree B2, the B2-W combines the stability of legged locomotion with the speed and efficiency of wheels, making it a highly versatile platform for dynamic and high-speed operations.
With a modular and expandable architecture, the B2-W robust payload capacity and power efficiency make it suitable for heavy-duty applications, including logistics automation, security patrol, and industrial inspection.
Engineered for durability, the B2-W features weather-resistant construction, long battery life, and wireless connectivity options like 5G and Wi-Fi, ensuring remote operation, real-time data transmission, and cloud-based processing. Whether deployed in warehouse automation, autonomous exploration, or collaborative robotic tasks, the Unitree B2-W sets a new standard for efficiency, versatility, and intelligence in modern robotics.
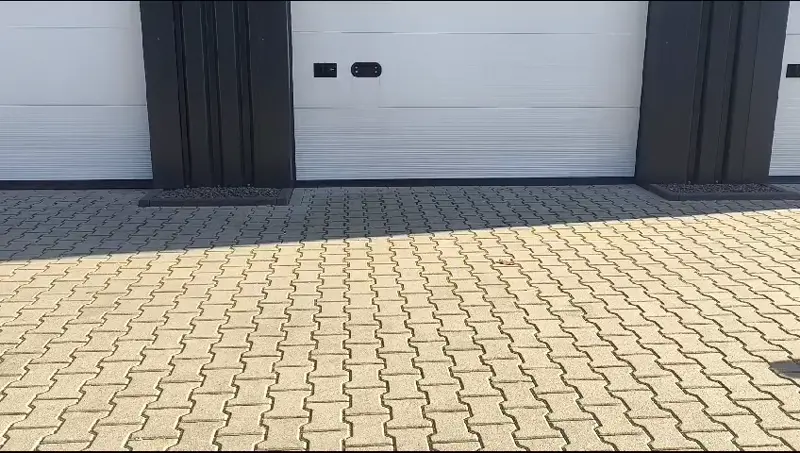
B2 Radar and Camera FOV
The B2 robot is equipped with advanced sensory systems, including the RS-Helios 5515 laser radar,D435i depth camera x2 and Optical Camera ×2 , which work in unison to provide superior environmental perception and spatial awareness.
RS-Helios 5515 Laser Radar
The RS-Helios 5515 laser radar is seamlessly integrated into the B2’s head, providing outstanding environmental sensing capabilities. Utilizing omnidirectional and full-angle scanning technology, it achieves a horizontal field of view (FOV) of up to 360° and a maximum vertical angle of 59°. This advanced lidar system enables the B2 to capture highly precise, real-time environmental data, generating detailed, high-resolution point cloud information. By rapidly detecting and measuring surrounding objects, the B2 ensures accurate and comprehensive spatial awareness, enhancing its ability to navigate and interact with complex environments efficiently.
D435i Depth Camera
The B2 is also equipped with two Intel RealSense D435i depth cameras, one positioned at the front and the other at the rear, further enhancing its visual perception capabilities. These cameras enable the robot to accurately perceive and interpret its surroundings, providing depth information for precise spatial awareness and obstacle detection. With this advanced vision system, the B2 can intelligently navigate complex environments, adapt to dynamic scenarios, and interact more effectively with its surroundings, ensuring optimal performance across a wide range of applications.
Combined FOV of RS-Helios 5515 and D435i
The integration of the RS-Helios 5515 laser radar and the D435i depth camera provides a merged field of view, enabling the B2 robot to achieve unparalleled environmental perception and adaptability. Together, these sensors ensure the B2 can operate effectively across diverse tasks and dynamic environments.
B2 User Interface Module
The top of the B2 is equipped with a variety of User interfaces, allowing seamless integration with body joint motors, sensor peripherals, network ports, and other expansion modules. This well-structured interface design enhances ease of use, facilitating efficient debugging, troubleshooting, and secondary development. By providing a flexible and user-friendly platform, the B2 enables developers to customize and extend its functionalities, making it suitable for a wide range of applications in research, industry, and robotics innovation.
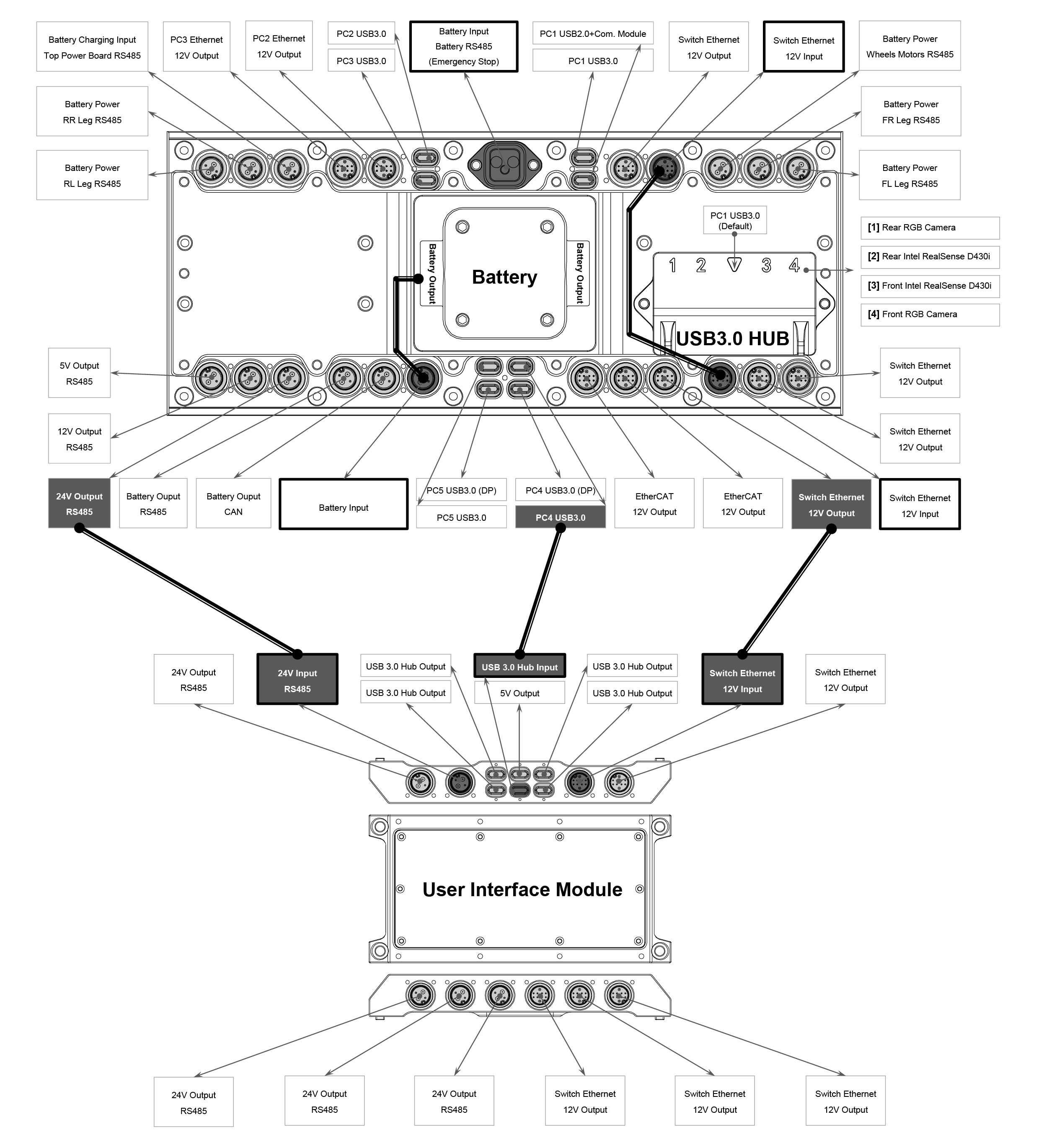
Top View of B2 Electrical Interface
Below is a description of the connectors and their respective interface specifications:
No |
Connector |
Interface Description (Short) |
Interface Specification |
---|---|---|---|
2 |
4x RS485 |
24V (2+2) Power Line Interface |
24V/10A power output |
3 |
Network |
12V (8+2) Signal Line Interface |
12V/10A power output Gigabit Ethernet (GbE) |
6 |
4x Type-C |
Type-C |
Supports USB3.0 host, 5V/1.5A power output |
10 |
5577 |
I/O OUT |
5V/3A power output |
B2 On-Board Computer
The B2 comes with a standard configuration featuring an Intel Core i5 processor for platform functions and an Intel Core i7 for user development. For enhanced performance, an optional configuration is available, offering an Intel Core i7 alongside up to three Nvidia Jetson Orin NX units, providing powerful computing capabilities for advanced applications and AI-driven tasks..
Development Computing Unit (PC 3)
Parameter |
Specification |
Model |
Jetson Orin NX |
CPU |
Arm® Cortex®-A78AE |
Number of Cores |
8 |
Number of Threads |
8 |
Maximum Clock Speed |
2 GHz |
Graphics Memory |
16 GB |
Total Memory |
16 GB |
Cache |
2 MB L2 + 4 MB L3 |
Storage |
2 TB |
Intel® Image Processing Unit |
Not Present |
GPU |
1024 NVIDIA Ampere Architecture GPUs with 32 Tensor Cores |
Maximum GPU Frequency |
918 MHz |
Gaussian and Neural Accelerator |
3.0 |
Intel® Deep Learning Boost |
Yes |
Intel® Adaptix™ Technology |
Yes |
Intel® Hyper-Threading Technology |
Yes |
Instruction Set |
64-bit |
OpenGL |
4.6 |
OpenCL |
3.0 |
DirectX |
12.1 |
IP Address |
192.168.123. |
Attention
The Operation and Control Computing Unit is solely designated for the Unitree motion control program and is not available for public access. Developers are only authorized to use the Development Computing Unit for secondary development. To obtain the initial user password, please refer to the FAQ.
In the table, the PC2 [Development Computing Unit] is assigned the IP address 192.168.123..
Additionally, the CPU modules may be shipped with a more advanced version, ensuring performance that meets or exceeds the listed specifications.
B2 Joint Motor
The B2 joint motor utilizes a self-developed Unitree motor that demonstrates exceptional performance and characteristics. With a maximum torque of 120 N·m, the motor features a hollow axis design, contributing to a more compact and lightweight structure. Additionally, the motor is equipped with dual encoders, enabling precise position and velocity feedback, which is essential for high-precision control requirements.
Joint Serial Number and Limits
The following table provides the joint indices, names, and respective joint limits in radians:
Index |
Joint Name |
Limit (rad) |
1 |
FL_Hip |
-0.87 ~ 0.87 |
2 |
FL_Thigh |
-0.94 ~ 4.69 |
3 |
FL_Calf |
-2.82 ~ 0.43 |
4 |
FR_Hip |
-0.87 ~ 0.87 |
5 |
FR_Thigh |
-0.94 ~ 4.69 |
6 |
FR_Calf |
-2.82 ~ 0.43 |
7 |
RL_Hip |
-0.87 ~ 0.87 |
8 |
RL_Thigh |
-0.94 ~ 4.69 |
9 |
RL_Calf |
-2.82 ~ 0.43 |
10 |
RR_Hip |
-0.87 ~ 0.87 |
11 |
RR_Thigh |
-0.94 ~ 4.69 |
12 |
RR_Calf |
-2.82 ~ 0.43 |
The image below displays the Unitree B2 robot with all joints labeled. It serves as a visual reference, correlating the joint listed in the table to their positions on the robot.
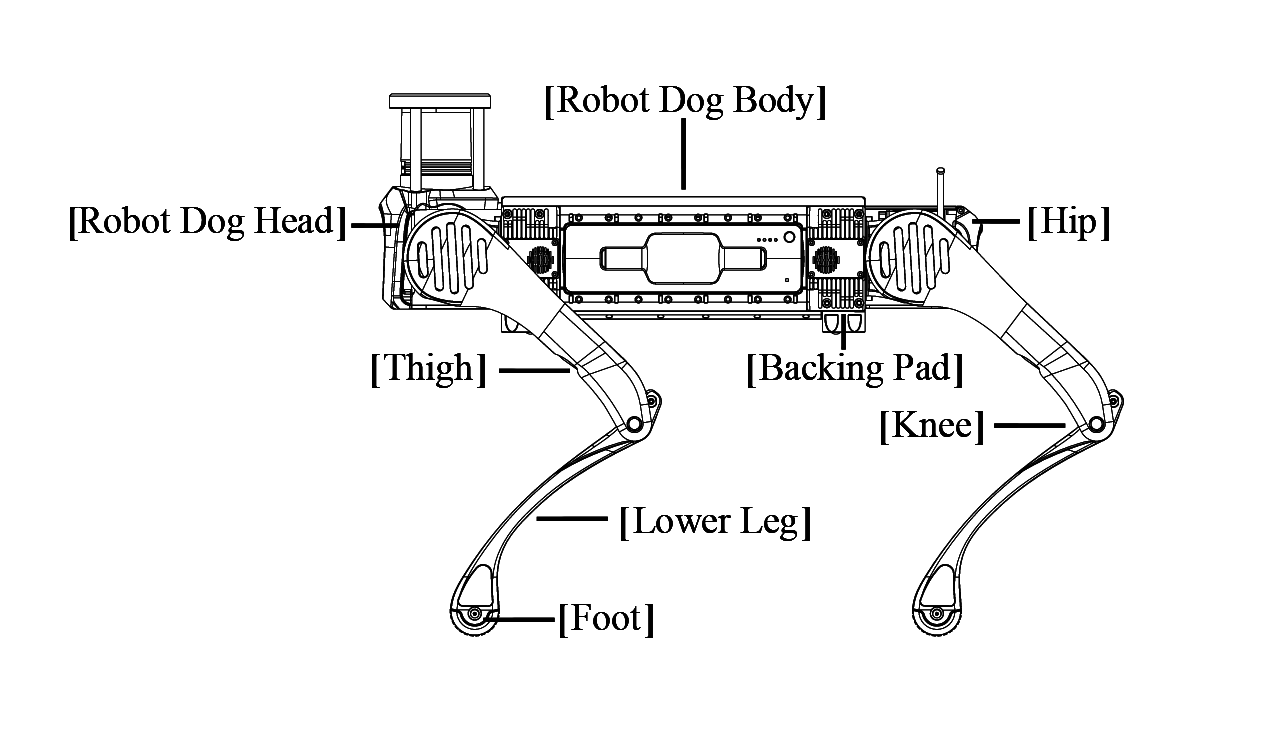
Reference Frame, Joint Axes, and Zero Position
When all joints are in their zero positions, the coordinate systems for the joints are as follows:
The X-axis is represented in red.
The Y-axis is represented in green.
The Z-axis is represented in blue.
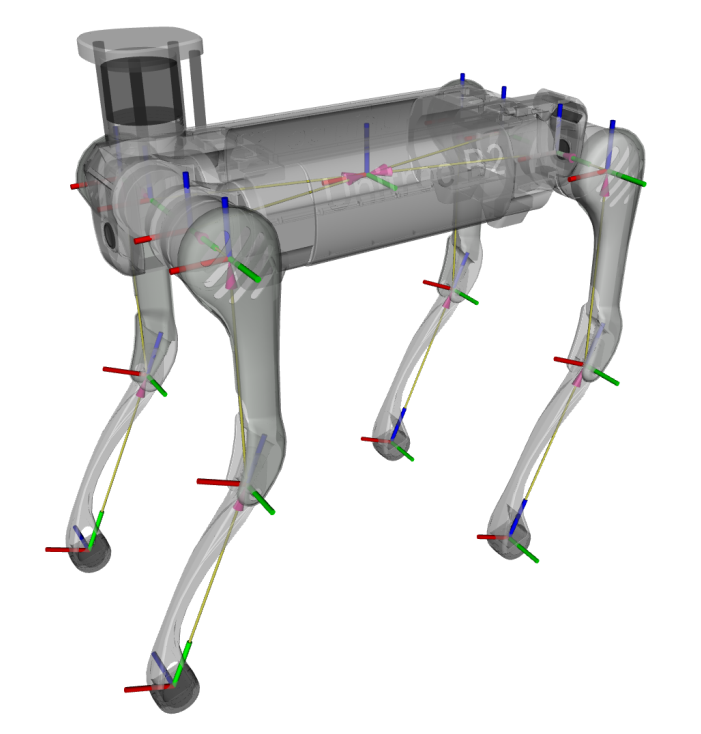